Ein Funitel ist eine kuppelbare Umlaufbahn, welche über zwei parallel und synchron laufende Förderseile verfügt. Speziell daran ist, dass die „Spurweite“ von ca. 3,2m der beiden Förderseile länger ist, als die Kabine breit ist. Der beim Funitel verbaute Gehängearm ist verglichen mit Pendelbahnen und Einseilumlaufbahnen extrem kurz. Ein grosser Vorteil an diesem System ist die Tatsache, dass bei extremen Windverhältnissen der Betrieb immer noch gewährleistet ist.
Eine technische Herausforderung besteht darin, dass beide Förderseile dauernd über die ganze Strecke exakt synchron laufen müssen. Es gibt zwei verschiedene Grundarten die Seilführung bei einem Funitel zu realisieren. Es sind dies die Systeme DMC (Double Mono Cable) und DLM (Double Loop Monocable). Beide unterscheiden sich nur geringfügig bei der Anzahl an Seilen, bzw. der Anzahl an Förderseilschlaufen. Beim DMC kommen zwei separate Fördeseilschlaufen zum Einsatz. Dies wiederum benötigt zwei einzelne Antriebe, welche je eine Antriebsscheibe mit genau gleichem Durchmesser besitzen müssen. Die Geschwindigkeit beider Förderseile werden durch die elektronische Steuerung überwacht und werden daher automatisch aufeinander stets während dem Betrieb aufeinander haargenau angepasst. Beim DLM kommt nur eine Förderseilschlaufe zum Einsatz. Ein sehr langes endloses Förderseil benötigt in der Theorie nur ein Antrieb und nur eine Antriebsscheibe. Durch die enormen Kräfte und länge des Seils kommen hierbei aber gegebenfalls ebenfalls zwei Antriebe und zwei Antriebsscheiben zum Einsatz. Ob jetzt ein DMC oder DLM eingesetzt wird, spielt für die Kuppelklemme keine Rolle.
-
-
Funitel in Verbier
-
-
DLM Antrieb Crans Montana
-
-
DLM Antrieb mit einer Förderseilschlaufe
Das erste Funitel wurde damals 1990 mit der DMC Technik im Skigebiet Val Thorens gebaut. Das Französische Plaungsbüro Dennis Creissels, sowie die Firma Städeli aus der Schweiz. waren massgeblich beteiligt an dem Projekt. Als die Firma Städeli 1991 durch Garaventa übernommen wurde, besass Garaventa ebenfalls die Möglichkeit, selbst Funitel’s zu erstellen. So entstand 1994 das erste Funitel Garaventa’s in Verbier. Das zweite und gleichzeitig auch das letzte jemals gebaute Funitel auf Schweizer Boden ging ein Jahr später in Crans Montana in Betrieb. Jenes Funitel besuchte ich im Juli 2018, von wo auch alle Bilder der Klemme stammen. Garaventa setzte nicht wie Creissels auf ein DMC, sondern auf das DLM System mit nur einer Förderseilschlaufe.
Die entworfene Kuppelklemme bei Creissels gleicht deren von Garaventa enorm, sie sind jedoch in der Funktion komplett anders. Der markante Unterschied besteht darin, dass Creissels’s Kuppelhebel zum öffnen der Klemme nach aussen gedrückt werden, die Kuppelhebel bei bei Garaventa jedoch nach innen. Beide Klemmen sind monostabil. Die hier vorgestellte Klemme zeigt nur jene von Garaventa, ich möchte die Tatsache aber dennoch mithilfe eines Bildes von www.funitel.de , welches die Kuppelstelle des Funitels in Val Thorens mit der Klemme von Creissels zeigt, beweisen. Vergleicht man beide Bilder, so erkennt man den Unterschied anhand der Anordnung der Kuppelschienen perfekt. Damit wäre bewiesen, dass es sich hier um zwei komplett verschiedene Klemmen handelt.
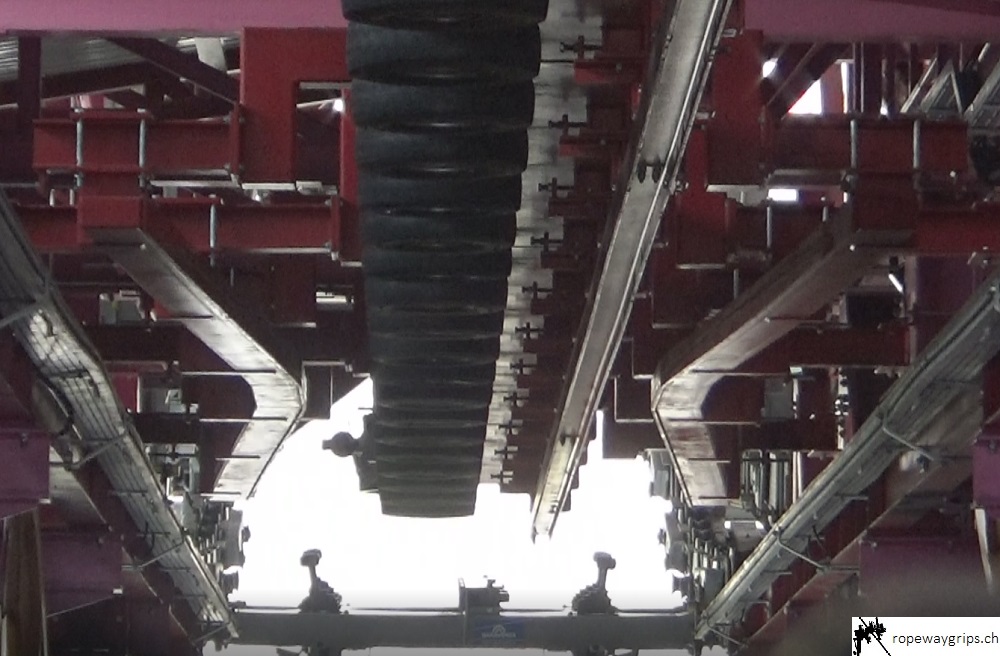
Kuppelstelle mit Klemmen von Garaventa
Nun zum eigentlichen Thema, der Kuppelklemme. Funitel verfügen pro Fahrbetriebsmittel über vier einzeln mechanisch zu betätigende Klemmen. Die in Crans Montana zum Einsatz kommende Klemme ist eine monostabile Schraubenfederklemme, dessen interessanterweise beide Klemmbacken beweglich sind. Von aussen erkennt man nicht, wie der Mechanismus der Klemme funktionieren soll. Bei meinem Besuch durfte ich die Klemme hautnah erkundigen und erkannte dann erst zu Hause mittels eine für mich gemachte Skizze richtig, wie sie denn wirklich funktioniert.
-
-
Funitel Kabine für 30 Pers.
-
-
Vier einzelne Kuppelhebel
Sobald der Kuppelhebel durch die markanten Kuppelschinen nach innen betätigt wird, wird zur selben Zeit die innere Klemmbacke mittels einer Zwangsöffnungsschiene angehoben. So wie ich das verstehe, dreht sich gleichzeitig die äussere Klemmbacke geringfügig nach aussen und lässt das Förderseil ohne Verschleiss entweichen oder packen. Die Innere Klemmbacke, ersichtlich auf dem vierten Bild, wird in der roten Pfeilrichtung angehoben. Der grüne Pfeil soll hervorheben, wie die innere Klemmbacke entriegelt wird.
-
-
Übersicht einer ganzen Klemme
-
-
Klemme öffnet in roter Pfeilrichtung
-
-
(Kopfachse) beide Klemmbacken sind beweglich
-
-
Innere Klemmbacke wird angehoben (roter Pfeil)
Um das ganze zu veranschaulichen, versuchte ich mich an einer Skizze der Klemme (keine Gewähr auf Vollständigkeit und Korrektheit):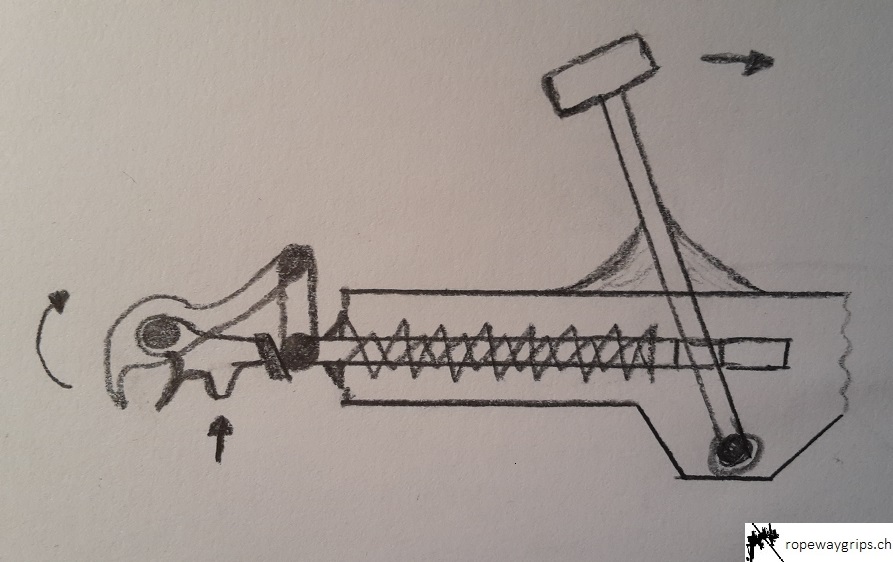
Sehr interessant ist auch, dass nicht wie üblich jeder Reifen eine eigene Drehzahl hat, sondern, dass alle miteinander mit dem gleichen Verhältnis verbunden sind. Ein Elektromotor verändert seine Geschwindigkeit und erhöht oder sinkt seine Drehzahl, sobald eine Kabine in der Beschleunigung- oder Verzögerungsphase angekommen ist.